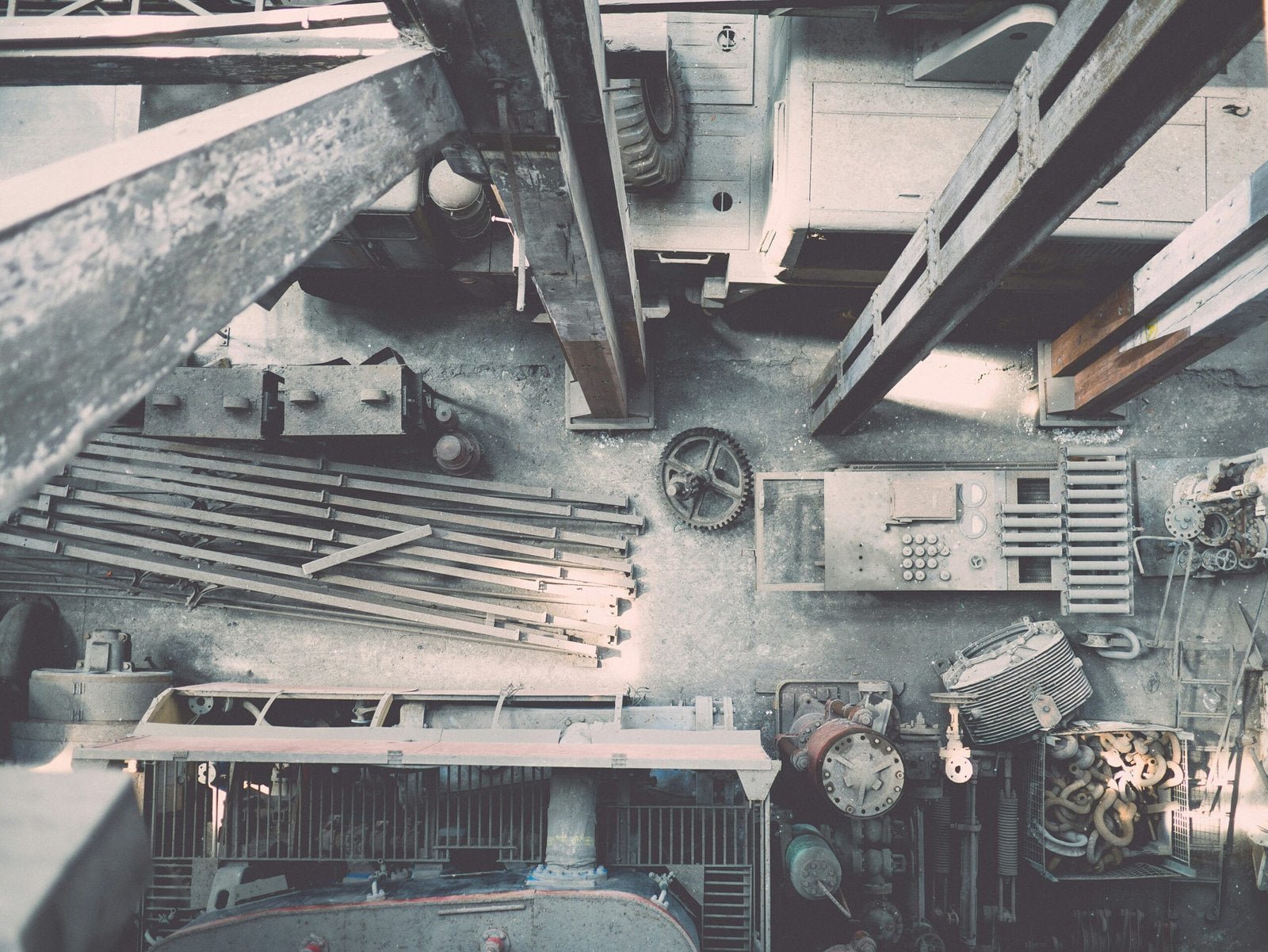
Introduction to Industrial Belts and Their Importance
Industrial belts are a pivotal component in various sectors due to their essential role in the transmission of power and movement. These belts come in several types, each designed to meet specific operational requirements. Prominent among them are timing belts, conveyor belts, and V-belts. Timing belts ensure synchronized movement between shafts, making them indispensable in precision-driven applications like automotive engines. Conveyor belts, widely used in logistics and material handling, facilitate the continuous movement of goods across distances. V-belts, known for their high friction and drive efficiency, are commonly deployed in machinery that requires power transmission over a short span.
In the manufacturing sector, industrial belts are fundamental in maintaining the seamless operation of assembly lines, affecting everything from productivity to product quality. In transportation, conveyor belts streamline the movement of luggage, packages, and other cargo. Agricultural machinery like harvesters and tractors heavily rely on these belts for various functions, directly impacting the efficiency and productivity of farming processes.
Given the demanding conditions in which these belts operate, they are subjected to significant wear and tear. The harsh operational environments, including exposure to extreme temperatures, chemicals, and abrasive materials, put enormous pressure on the belts’ performance and durability. As such, the use of high-quality materials like rubber is crucial. Rubber offers excellent tensile strength, flexibility, and resistance to environmental stressors, thereby enhancing the lifespan and reliability of industrial belts.
The construction and design of these belts are continually evolving to meet the ever-increasing performance demands. Manufacturers are consistently innovating, utilizing advanced materials and state-of-the-art technologies to produce belts that can stand up to the rigorous demands of modern industry. This underscores the importance of industrial belts not just as components, but as critical enablers of efficient and effective operation across numerous sectors.
Why Rubber is a Preferred Material in Industrial Belts
Rubber is a cornerstone material in the construction and manufacturing of industrial belts, owing to its distinctive properties that enhance performance and durability. Primarily, rubber’s elasticity ensures that industrial belts maintain flexibility under varying load conditions. This elasticity is crucial as it allows the belt to adapt to different operational stresses without losing its shape, ensuring consistent performance.
Additionally, rubber’s inherent flexibility significantly contributes to the smooth operation of industrial machinery. This characteristic allows the belts to bend around pulleys and other components without cracking or breaking, facilitating a seamless transfer of power and reducing the need for frequent replacements.
Another pivotal property of rubber is its resistance to wear and tear. Industrial environments often subject belts to abrasive conditions, which can quickly degrade materials lacking inherent durability. Rubber, however, exhibits robust resistance to such wear, extending the lifespan of the belts and enhancing their reliability in industrial applications.
The choice of rubber type also plays a vital role depending on specific industrial requirements. Natural rubber, known for its excellent tensile strength and resilience, is often used in applications where elasticity and flexibility are paramount. On the other hand, synthetic rubbers such as neoprene, nitrile, and ethylene propylene diene monomer (EPDM) offer unique benefits. For example, neoprene is highly resistant to oils and chemicals, making it suitable for environments where such substances are prevalent. Nitrile rubber, with its superior resistance to oils and some chemicals, is commonly used in manufacturing settings that deal with harsh substances. EPDM excels in resisting weathering, ozone, and harsh temperatures, making it ideal for outdoor applications or environments with extreme temperature variations.
These characteristics underscore why rubber remains a preferred material in the industrial belt sector. Its unique combination of elasticity, flexibility, and resistance to wear and tear not only enhances the belts’ performance but also ensures their durability, making it indispensable in diverse industrial settings.
Manufacturing Process of Rubber Industrial Belts
The manufacturing process of rubber industrial belts is a meticulous and multifaceted procedure aimed at ensuring optimal performance and durability. It begins with the careful selection and preparation of raw materials. Natural and synthetic rubber forms the primary component, chosen based on the specific requirements of the belt, including flexibility, strength, and resistance to environmental factors. The raw rubber is then cleaned, cut, and weighed to precise specifications to form the base mixture.
Following preparation, the rubber enters the mixing phase, where it is compounded with various additives such as carbon black, antioxidants, and accelerants. This mixture is rigorously blended to create a homogeneous compound with enhanced properties suited for industrial application. The compounded rubber is then subjected to a curing process, which involves heating the mixture at high temperatures to initiate chemical reactions that solidify the material, significantly enhancing its resilience and elasticity.
Reinforcement materials play a crucial role in fortifying the belts. Polyester, aramid, or high-tensile steel cords are commonly integrated into the rubber matrix during the manufacturing process. These reinforcements offer supplementary strength and resistance to stretching, thus extending the belt’s operational lifespan in high-stress environments. The precise alignment and embedding of these materials are critical to achieving the desired belt characteristics.
Extrusion and molding are the subsequent key stages. The compounded rubber is extruded through a die to create a continuous belt shape, following which precise molding techniques shape the belts to their final dimensions. To further enhance the rubber’s mechanical properties, the vulcanization process is employed. Vulcanization involves heating the moulded belts with sulfur or other crosslinking agents, which form cross-links between polymer chains, significantly boosting the material’s temperature resistance, tensile strength, and durability.
Throughout the manufacturing process, stringent quality control measures are implemented to ensure the industrial belts meet high standards of performance and reliability. These measures include rigorous inspection for material consistency, tensile strength testing, and thorough evaluation of finished products under simulated operational conditions. By employing a comprehensive and controlled manufacturing process, the rubber industry ensures that the constructed belts deliver consistent and reliable performance, capable of withstanding the demands of various industrial applications.
Advantages and Applications of Rubber Industrial Belts
Rubber industrial belts offer multiple advantages that make them indispensable in various sectors. A primary benefit is their excellent shock absorption capabilities. In industries such as automotive and heavy machinery, the rubber belts’ potential to dampen vibrations can prolong the lifespan of both the belt and the machinery. This characteristic is vital for reducing wear and tear on other integral components, thereby facilitating smoother operation and lowering maintenance costs.
Chemical resistance is another prominent advantage of rubber belts. In food processing industries, for instance, rubber materials come into contact with different substances, including cleaning agents and food products. The chemical-resistant properties of rubber ensure that the belts do not degrade or lose functionality, maintaining hygiene standards and durability. Furthermore, the ability to resist a range of chemicals broadens their application in pharmaceutical and petrochemical industries.
Rubber belts also excel in extreme temperature conditions. Their ability to function efficiently under both high and low temperatures makes them suitable for diverse environments, from the cold storage units in food processing to the high-heat conditions often found in manufacturing plants. This versatility enhances the reliability and performance of industrial operations.
Industries such as automotive, food processing, and heavy machinery heavily rely on rubber belts. For example, in the automotive sector, rubber belts facilitate the efficient transmission of power in engines, while in food processing, they ensure smooth and hygienic movement of items across production lines. Heavy machinery operations benefit from rubber belts’ robust performance in demanding conditions, aiding in the seamless movement of heavy loads.
In terms of maintenance, rubber belts generally require minimal upkeep, contributing to cost-effectiveness over time. Regular inspection for wear and tear, proper alignment, and timely lubrication can significantly extend their life expectancy. Typically, rubber belts can last from several months to several years, depending on the application and maintenance practices. The long lifespan and reduced need for constant replacement or repair make them a cost-effective choice for various industrial applications.