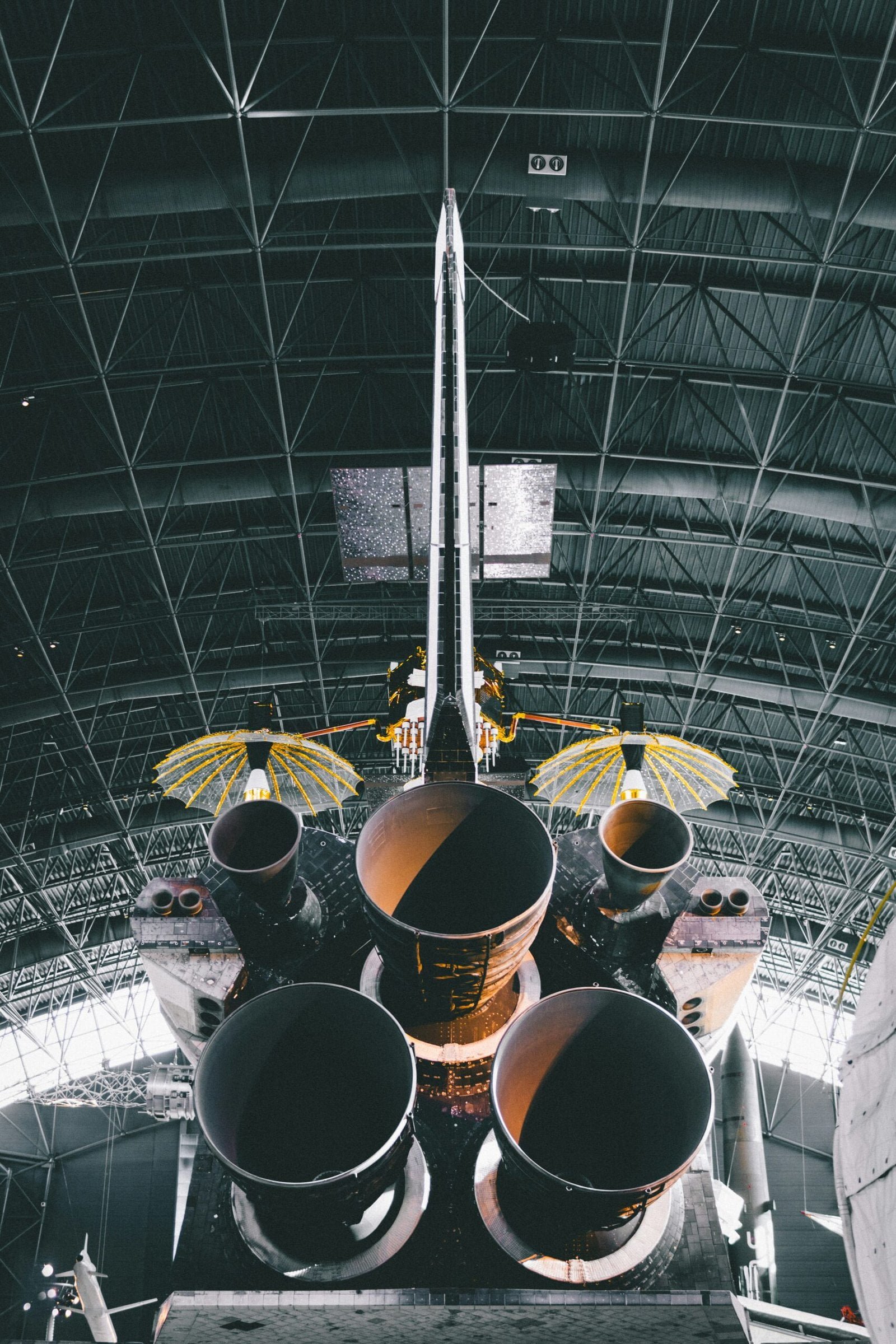
Introduction to Rubber in Aerospace Engineering
Rubber, a versatile and resilient material, has long been a crucial component in the field of aerospace engineering. Its unique properties, including elasticity, temperature resistance, and durability, make it a suitable choice for various aerospace applications. Historically, the use of rubber in aerospace engineering dates back to the early 20th century, when it was first utilized for sealing and insulation purposes in aircraft.
One of the primary attributes of rubber that enhances its utility in aerospace is its elasticity. This characteristic allows rubber to absorb and dissipate energy, making it ideal for applications that require shock absorption and vibration damping. For instance, rubber components are often used in landing gear systems to cushion the impact of landing, thereby enhancing the longevity and reliability of these critical systems.
Temperature resistance is another significant property of rubber that contributes to its widespread use in aerospace engineering. Aircraft and spacecraft operate in extreme temperature environments, ranging from the freezing conditions of high altitudes to the scorching heat generated by engine components. Rubber’s ability to maintain its integrity and performance across a wide temperature spectrum ensures that it can reliably perform in these challenging conditions. Specialized rubber compounds, designed to withstand these extreme temperatures, are commonly used in seals, gaskets, and hoses.
Durability is a further advantage of rubber in aerospace applications. The demanding nature of aerospace operations requires materials that can endure constant stress and wear. Rubber’s high resistance to abrasion, chemicals, and environmental factors makes it an excellent choice for long-lasting components. For example, rubber seals and gaskets play a vital role in maintaining the integrity of fuel systems, hydraulic systems, and cabin pressure.
Technological advancements have continuously expanded the applications of rubber in aerospace engineering. The development of synthetic rubbers, such as silicone and fluorocarbon rubber, has provided engineers with materials that offer enhanced performance characteristics. These modern rubber compounds can withstand even more extreme conditions and provide improved resistance to aging and degradation.
In essence, rubber’s exceptional properties of elasticity, temperature resistance, and durability make it an indispensable material in aerospace engineering. Its historical significance and ongoing advancements ensure that it will continue to play a pivotal role in enhancing the performance and durability of aerospace systems.
Types of Rubber Materials Used in Aerospace
In the realm of aerospace engineering, the selection of rubber materials plays a pivotal role in ensuring the performance and durability of various components. Among the diverse array of rubber materials utilized, natural rubber and synthetic rubbers such as silicone, nitrile, and fluorocarbon stand out due to their distinct properties and advantages.
Natural rubber, derived from the latex of rubber trees, is prized for its excellent elasticity, tensile strength, and abrasion resistance. However, its susceptibility to weathering and temperature variations limits its application in aerospace engineering to non-critical components or those that operate under controlled conditions.
Synthetic rubbers, on the other hand, offer a broader range of properties tailored to meet the stringent demands of aerospace applications. Silicone rubber, for instance, is highly valued for its exceptional thermal stability, remaining flexible at temperatures as low as -55°C and as high as 300°C. This makes it ideal for seals, gaskets, and insulation in environments exposed to extreme temperatures.
Nitrile rubber, also known as Buna-N, is renowned for its resistance to oils, fuels, and other chemicals, making it suitable for use in fuel system components and hydraulic hoses. Its durability and resilience under mechanical stress further enhance its applicability in aerospace engineering.
Fluorocarbon rubber, commonly referred to as FKM or Viton, offers superior resistance to high temperatures, chemicals, and ozone. Its remarkable stability under harsh conditions makes it an excellent choice for O-rings, seals, and gaskets in critical aerospace systems where reliability and longevity are paramount.
The manufacturing processes and treatments these rubbers undergo are equally critical in meeting aerospace standards. Techniques such as vulcanization enhance the mechanical properties and thermal stability of rubber materials, while specialized coatings and treatments improve their resistance to environmental factors like UV radiation and ozone. Rigorous testing and quality control measures ensure that the rubber components meet the stringent performance and safety standards required in the aerospace industry.
In summary, the diverse types of rubber materials used in aerospace engineering, along with advanced manufacturing processes, significantly contribute to the reliability and performance of aerospace components. The careful selection and treatment of these materials are essential in addressing the unique challenges posed by the aerospace environment.
Applications of Rubber in Aerospace Components
Rubber plays a crucial role in the aerospace industry, providing essential functionalities that enhance both performance and durability. In aerospace engineering, rubber is utilized in various components, each serving a specific purpose to ensure the safety and efficiency of aerospace vehicles.
One of the primary applications of rubber in aerospace is in seals and gaskets. These components are vital for maintaining the integrity of aircraft systems by preventing leaks of fluids and gases. Rubber’s elasticity and resilience make it an ideal material for creating tight seals that can withstand extreme temperatures and pressures. For instance, O-rings made from specialized rubber compounds are used extensively in fuel systems, hydraulic systems, and landing gear, ensuring operational safety and reliability.
Rubber is also extensively used in hoses within aerospace systems, where flexibility and resistance to harsh environmental conditions are paramount. Aerospace hoses must endure significant thermal cycling, chemical exposure, and mechanical stress. Rubber hoses, often reinforced with other materials, are crucial for the efficient transfer of fluids and gases, including fuel, hydraulic fluids, and coolants, thereby contributing to the overall functionality of the aircraft.
Vibration dampeners are another critical application of rubber in aerospace engineering. Aircraft are subjected to various sources of vibration and noise, which can affect both performance and comfort. Rubber-based vibration dampeners help to absorb and minimize these vibrations, protecting sensitive equipment and enhancing the longevity of components. This application is particularly significant in the context of avionics and other precision instruments.
Insulation is yet another domain where rubber finds its application in aerospace. Rubber materials are used to insulate electrical wiring and components, providing protection against electromagnetic interference (EMI) and ensuring electrical safety. Additionally, rubber insulation helps in thermal management, maintaining optimal operating temperatures for various systems.
Real-world examples underscore the effectiveness of rubber in aerospace. For instance, the Space Shuttle program employed rubber O-rings in its solid rocket boosters, although the tragic Challenger incident highlighted the critical importance of material selection and quality. More successful applications include the use of rubber in the Boeing 787 Dreamliner’s advanced sealing systems, which contribute to the aircraft’s fuel efficiency and performance.
In conclusion, the diverse applications of rubber in aerospace components underscore its indispensable role in ensuring the performance, safety, and durability of aerospace vehicles. From seals and gaskets to hoses, vibration dampeners, and insulation, rubber’s unique properties make it a vital material in the advancement of aerospace engineering.
Future Trends and Innovations in Rubber Technology for Aerospace
The advancement of rubber technology is pivotal for the aerospace industry, promising enhancements in performance and durability. One of the most exciting trends is the development of new rubber composites that offer superior characteristics compared to traditional materials. These composites often integrate carbon nanotubes or graphene, which provide exceptional strength, flexibility, and thermal stability, making them ideal for aerospace applications. As a result, components made from these advanced rubber composites can withstand extreme conditions, thereby increasing the overall durability and reliability of aerospace systems.
Manufacturing techniques are also evolving, with innovations such as 3D printing and additive manufacturing gaining traction. These methods allow for more precise and complex designs, reducing material waste and enabling the production of custom rubber components tailored to specific aerospace needs. Furthermore, advancements in vulcanization and curing processes are leading to rubber materials with enhanced performance properties, such as improved resistance to wear, chemicals, and temperature variations.
Sustainability is another key focus area in the future of rubber technology for aerospace. Researchers are exploring the use of bio-based rubbers, derived from renewable resources, as an eco-friendly alternative to traditional synthetic rubbers. These sustainable materials not only reduce the environmental impact but also have the potential to offer comparable, if not superior, performance attributes. Additionally, recycling initiatives are being developed to reclaim rubber from decommissioned aerospace components, further contributing to a circular economy.
The potential impact of these innovations on aerospace engineering is profound. Improved rubber materials and manufacturing techniques can lead to lighter, more efficient, and longer-lasting components, ultimately enhancing the performance and durability of aerospace systems. As these trends continue to evolve, the integration of advanced rubber technologies will play a crucial role in the future success of the aerospace industry, driving forward both technological progress and sustainability.