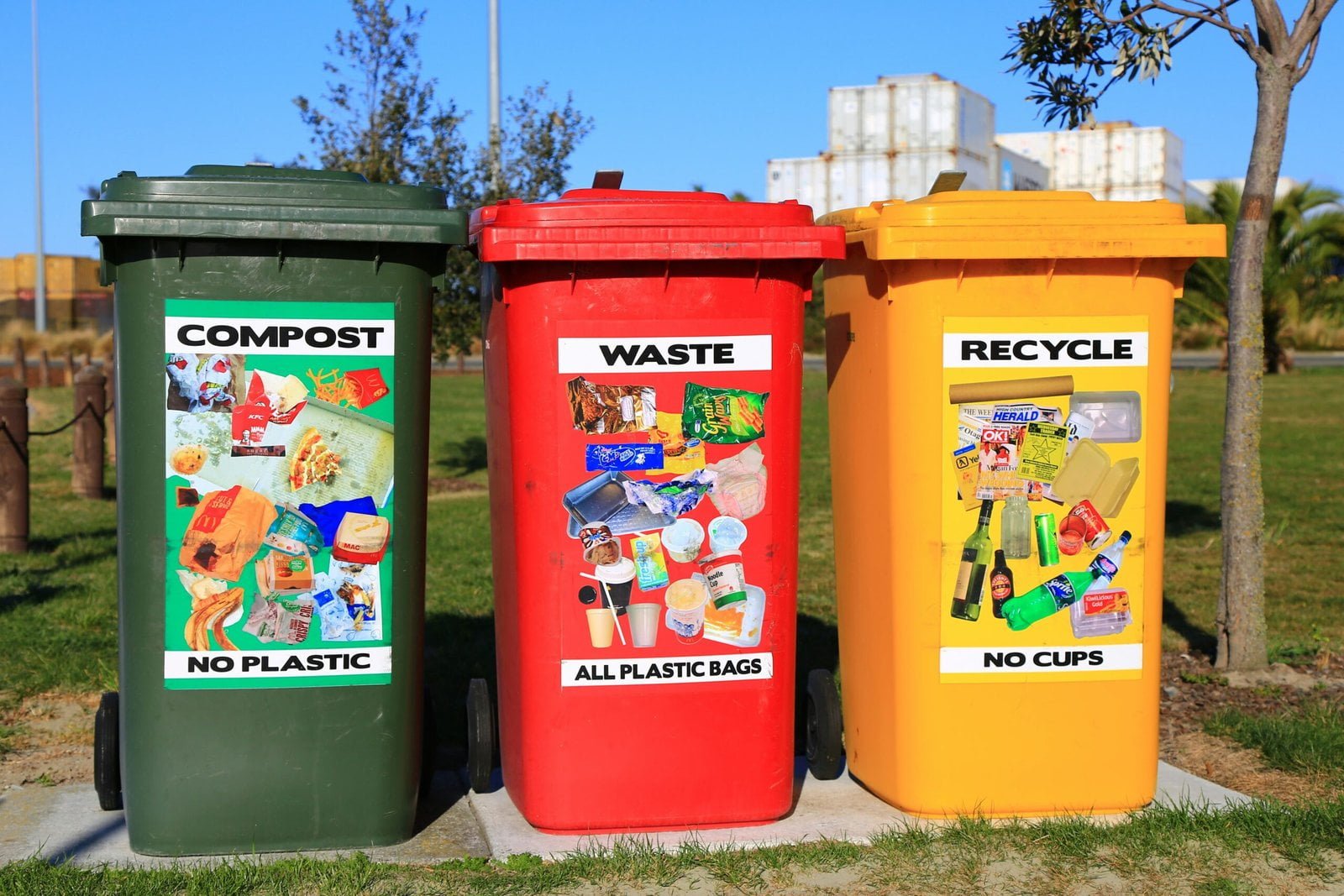
Introduction to PVC Recycling
Polyvinyl chloride, commonly known as PVC, is one of the most widely used plastics in the world. Its versatility and durability make it an essential material in various industries, including construction, healthcare, and consumer goods. PVC is frequently found in products such as pipes, electrical cable insulation, flooring, and medical devices, among others. Consequently, the production and consumption of PVC generate significant quantities of waste, necessitating effective recycling strategies.
Recycling PVC holds paramount importance due to the environmental concerns associated with its disposal. Conventional methods of PVC disposal, such as landfilling and incineration, pose substantial risks. Landfilled PVC can leach hazardous chemicals into the soil and groundwater, while incineration releases toxic dioxins and furans into the atmosphere. Therefore, minimizing the environmental footprint of PVC through efficient recycling methods is crucial for sustainable development.
However, recycling PVC presents several challenges. The material’s composition often includes additives like plasticizers, stabilizers, and impact modifiers, which complicate the recycling process. Additionally, separating PVC from other plastics in mixed-waste streams is not always straightforward. Despite these challenges, advancements in PVC recycling technologies are making it increasingly feasible to recycle PVC waste efficiently and effectively. Emerging methods and innovations are addressing the technical and economic hurdles, thus facilitating a more sustainable approach.
This evolving landscape of PVC recycling technologies is a testament to the industry’s commitment to sustainability and environmental protection. The next sections will delve deeper into these advancements, exploring both established and cutting-edge methods that are shaping the future of PVC recycling. From mechanical recycling to chemical processes and innovative technologies, understanding these developments is key to fostering a circular economy for PVC.
Mechanical Recycling Methods
Mechanical recycling methods have long been the cornerstone of the PVC recycling industry. These methods involve the collection, separation, cleaning, and reprocessing of PVC waste into new material. Initially, collected PVC waste is sorted to remove contaminants and other non-PVC materials. Advanced sorting technology, such as near-infrared (NIR) systems, have significantly improved the accuracy and efficiency of this step, enabling more precise separation and higher quality outputs.
Once sorted, the PVC undergoes thorough cleaning processes to remove any residual impurities. Mechanical techniques such as shredding and grinding transform the cleaned PVC into smaller, more manageable pieces. These particles are then melted and reformed into granules or pellets, which can be reintroduced into manufacturing streams to create new PVC products.
However, mechanical recycling is not without its limitations. One of the primary concerns is the degradation of material quality over repeated recycling cycles. PVC can lose its structural integrity and desirable properties due to thermal and mechanical stresses during processing. This degradation often necessitates the use of virgin PVC material to maintain product standards, thus limiting the sustainability of recycled PVC.
Recent technological advancements aim to mitigate these issues and enhance the performance of mechanical recycling. Innovations in purification processes, such as advanced screening and filtration techniques, enable the removal of finer impurities, leading to higher quality recycled PVC. Additionally, scalable solutions for industrial applications have emerged, facilitating the mechanical recycling process on a larger scale and making it more economically viable for businesses.
Overall, while mechanical recycling methods face challenges, continuous advancements in technology underscore the industry’s commitment to improving sustainability. By integrating cutting-edge sorting, cleaning, and purification systems, the mechanical recycling of PVC can become more efficient and effective, contributing positively to the circular economy model.
Chemical Recycling Technologies
The field of PVC recycling is undergoing significant advancements, particularly in the realm of chemical recycling. Chemical recycling methods offer a transformative approach by breaking down polyvinyl chloride (PVC) into its original monomers or other useable chemicals. This method not only minimizes waste but also paves the way for producing high-quality recycled plastics that maintain the integrity of virgin material.
One of the most promising chemical recycling techniques is pyrolysis. Pyrolysis involves heating PVC in the absence of oxygen, which decomposes it into useful products like hydrochloric acid and hydrocarbon fractions. The main advantage of pyrolysis is its ability to handle mixed waste streams and contaminants, which are often a challenge for mechanical recycling processes. However, the high energy requirement and the potential release of harmful substances pose challenges that need to be carefully managed.
Another noteworthy technique is hydrolysis, which uses water to break down PVC into its constituent chemicals. Hydrolysis generally occurs under high temperatures and pressures, resulting in the formation of ethylene glycol and hydrochloric acid. The principal benefit of hydrolysis is the purity of the resulting chemicals, which can be directly reused in manufacturing new PVC products. Nevertheless, the process’s complexity and the need for specialized equipment can be limiting factors in its broader adoption.
The practical potential of these chemical recycling methods is being demonstrated through various pilot projects and commercial applications. For instance, a notable pilot project in Europe successfully utilized pyrolysis to convert mixed plastic waste into valuable chemicals, achieving significant reductions in greenhouse gas emissions. Another commercial application in Japan has shown that hydrolysis can be scaled up effectively, combining economic viability with environmental sustainability.
While these technologies present promising pathways for the future of recycling within the PVC industry, they also carry certain challenges, including high operation costs and stringent regulatory requirements. Continued research and development, alongside supportive policy frameworks, are crucial for overcoming these hurdles and realizing the full potential of chemical recycling methods.
Future Trends and Challenges in PVC Recycling
The landscape of PVC recycling is poised for significant evolution, driven by advances in technology, regulatory shifts, and market dynamics. Among the forefront of emerging innovations are smart sorting systems, which leverage artificial intelligence and robotics to enhance the efficiency and purity of recycled materials. These systems promise to reduce contamination rates and improve the quality of recycled PVC, thus facilitating its reusability in higher-end applications.
Another promising development is the advent of new catalysts that are fostering advancements in chemical recycling. These catalysts can break down PVC into its constituent monomers, enabling the creation of virgin-quality plastics. This technological breakthrough holds the potential to overcome some of the limitations of traditional mechanical recycling methods, which often result in downcycled materials of lower quality.
Circular economy models are also gaining traction within the PVC recycling industry. These models emphasize the importance of designing products with their end-of-life in mind, thus facilitating easier recycling and reducing overall waste. Companies are increasingly adopting these principles by developing take-back schemes and enhancing the recyclability of their products from the design stage.
However, the path forward is not without challenges. Economic feasibility remains a significant barrier; the costs associated with advanced recycling technologies and systems can be prohibitive for widespread adoption. Additionally, there is a pressing need for comprehensive and supportive legislation to drive the industry’s progression. Policymakers must create frameworks that incentivize recycling efforts and regulate the use of virgin PVC where viable alternatives exist.
Industry experts predict that collaborative efforts between stakeholders, including manufacturers, recyclers, governments, and consumers, will be crucial in overcoming these hurdles. Potential breakthroughs, such as more cost-effective recycling processes and greater regulatory support, could transform PVC recycling from a niche segment into a mainstream industry. This would substantially influence the sustainability of plastic production and consumption on a global scale.